Vacuum & Controlled Atmosphere Melting
Vacuum and controlled atmosphere melting systems are used for the world’s most demanding casting applications. The creation and casting of super alloys and many other advanced and reactive metals requires sophisticated vacuum or controlled atmosphere melting and remelting systems. Many high quality specialty metals and materials are produced and refined using Inductotherm melting systems.
Vacuum Induction Melting (VIM) furnaces are used to produce high-quality castings that cannot be feasibly created in an air atmosphere.
Key Benefits of Vacuum Precision Casting Furnaces
The use of vacuum technology in precision casting provides a number of key benefits in terms of quality and consistency in the castings produced:
- Eliminates environments that would promote the reaction of the liquid metal with oxygen/nitrogen.
- Reduces porosity created by gas entrainment within the casting.
- Ability to directly influence the metal solidification through control of the cooling mechanism.
TYPES OF FURNACES MOST OFTEN USED IN VACUUM CHAMBERS
- Heavy Steel Shell Furnaces
- Small-Capacity Steel Shell Furnaces
- Dura-Line® Furnaces
- Double-Trunnion
- Box Furnaces
- Coax Furnaces
- Nose-Tilt Furnaces
- Tilt-PourTM Furnaces
VIM Is Perfect for Producing:
- Nickel and Cobalt Based Superalloys
- Stainless Steels and Specialty Steels
- Magnetic and Battery Alloys
As the world’s leading manufacturer of induction metal melting systems for metal producers today, Inductotherm has built more than 38,500 melting and heating systems for metal and metalcasting producers around the globe.
Inductotherm offers our clients the industry’s highest level of expertise, support, and services. Contact us anytime.
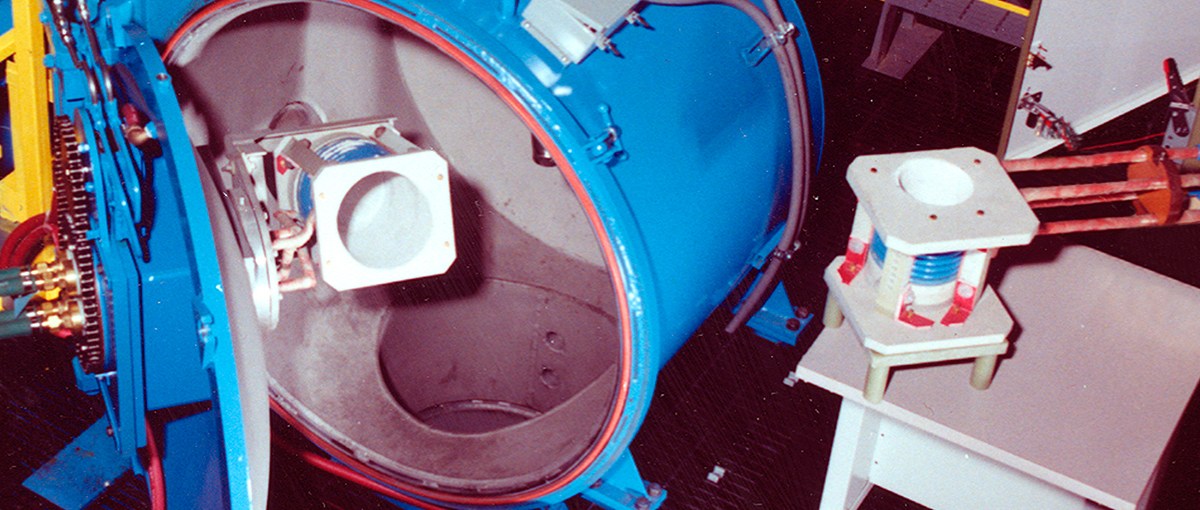
Inductotherm Vacuum Induction Melting (VIM) Furnaces are designed specifically for operation in high vacuum environments and include vacuum-adapted construction methods and the industry’s most advanced coil and connector dielectric insulation technologies and procedures.
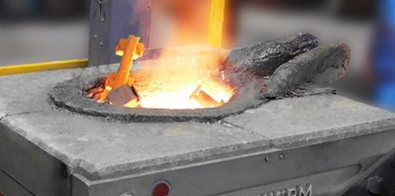
Dura-Line® induction melting furnaces are ideal for when you want big furnace features in a midsize induction furnace melter.