Iron Melting
We offer equipment designed for virtually every iron charging, melting, holding and pouring operation.
The leading manufacturer of agricultural machinery, the world’s largest producer of ductile iron pipe, and a leading builder of cast iron bathtubs are just a few examples of the worldwide industry leading companies who rely on iron melting, holding, and pouring systems built by Inductotherm. In fact, walk into an induction iron foundry anywhere in the world and you are likely to find that its melt shop is equipped with lnductotherm furnaces and power supplies. You also are likely to find lnductotherm automated controls, material charging systems and automated pouring systems. Inductotherm is the only supplier who manufactures all of these systems. We are a one stop shop.
We offer a broad range of furnace sizes and types, as well as a full range of energy efficient induction power supplies. Whether a foundry needs a small hand-tilted furnace for 2 kg castings or a 20 ton furnace ready to pour every half-hour, Inductotherm offers appropriately sized induction equipment with a guaranteed melt rate and a foundry-proven design.
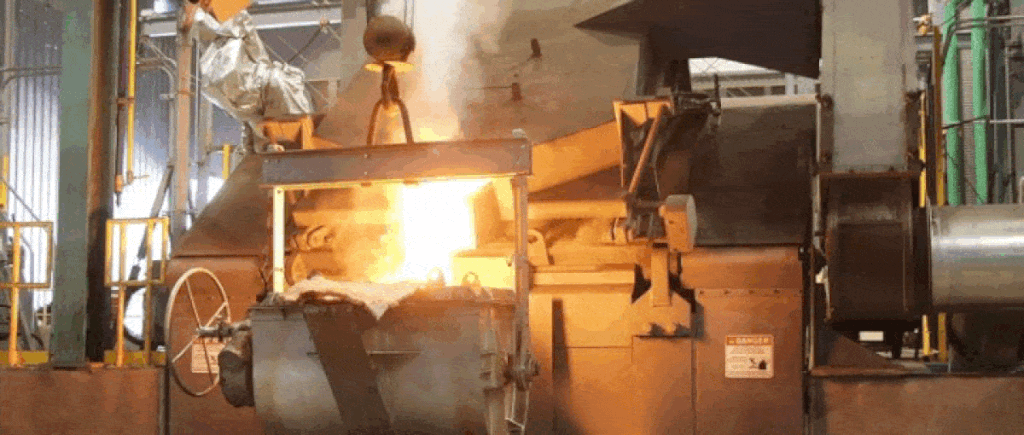
Our high power density, heavy steel shell coreless furnaces and efficient VIP® power supplies are leading a productivity revolution in high-production foundries.
Together with Inductotherm automation technologies for material charge drying/preheating, furnace charging, alloy batch preparation, computer control, fume collection and lining removal, these systems are increasing casting production while reducing energy and labor costs.
Inductotherm dual-output and multiple-output induction power supplies enable foundries to optimize the flexibility and efficiency of their melting operations by increasing power supply utilization approaching 100 percent. These systems also help foundries use power more efficiently for melting and holding without increasing electric utility demand charges.
On the mold line, Inductotherm’s high-speed automated pouring systems include both unheated tundish units and inductively heated pressure pour furnaces for gray and ductile iron. These designs feature adaptive and precise stopper-rod pouring mechanisms for lines pouring in excess of 400 molds per hour.
Inductotherm melt shop and automated pouring systems, like infrastructure castings themselves, are built for rugged durability, practical maintenance and long service life. High quality is essential in casting malleable and ductile iron pipe fittings, valves and pump components.
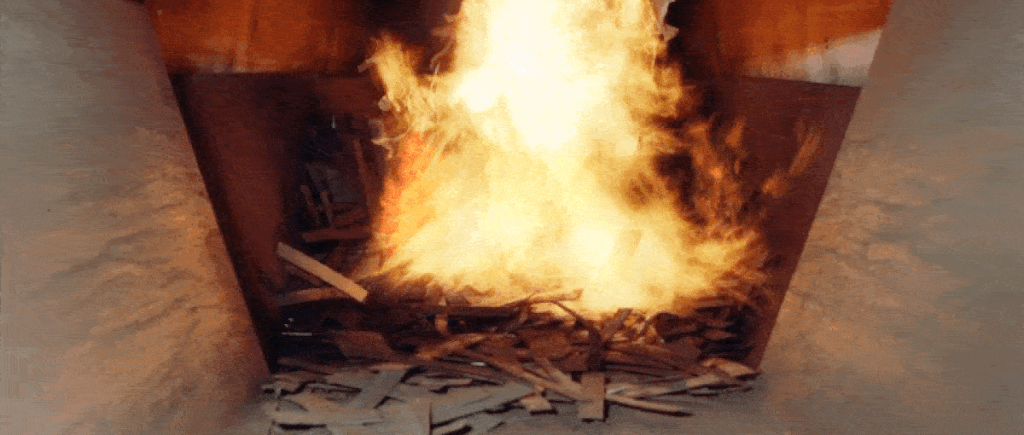
Inductotherm customers melt substantial quantities of metal to produce gray and ductile iron pipes, pipe fittings and connectors, municipal castings, electrical boxes and other infrastructure castings. Inductotherm scrap drying and automated charging systems enhance safety and keep pace with melting operations. High-capacity heavy steel shell coreless melting furnaces, coreless holding furnaces and channel holding furnaces assure a steady supply of on-specification molten iron.
Inductotherm Meltminder® computer systems allow furnace operators to manage melting operations more precisely and safely while automating the collection of key performance data.
Recognizing that working on a melt deck is hard and sometimes dangerous, Inductotherm developed equipment that is designed to keep people away from molten metal. The ARMS™ (Automated Robotic Melt Shop) system is designed to perform all the dangerous melt deck operations such as slagging, temperature taking, metal sampling, making alloy additions, and verifying proper grounding.
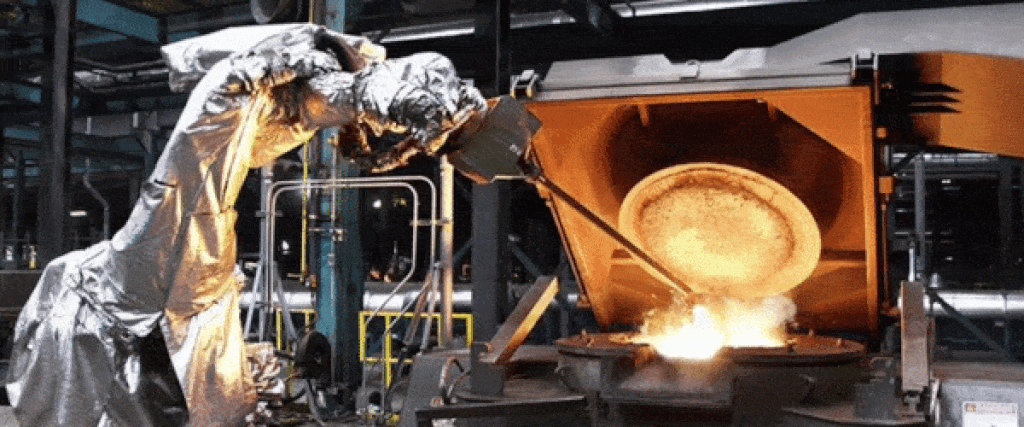
Complete Systems for Melting Iron
More than Furnaces
- Automated Pouring
- Material Handling
- Induction Power Supplies
- Computer Control Systems
- Robotic Slagging
- Water Cooling Systems
Contact us today to speak with an iron melting expert.
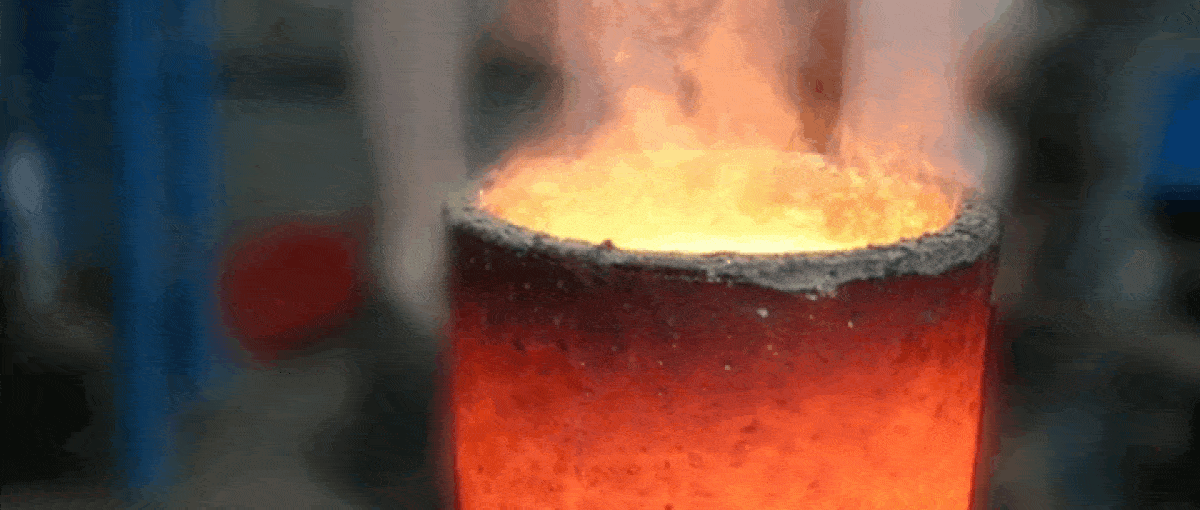
Inductotherm induction furnaces offer superior performance and outstanding durability for all your melt shop needs regardless of the size of your foundry, melt shop or facility.
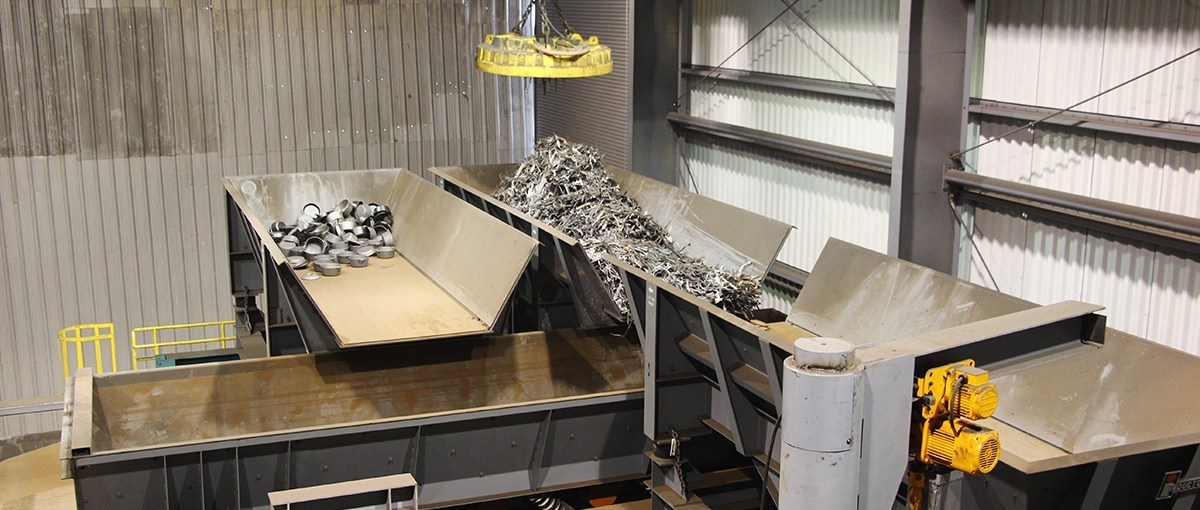
Our material handling systems are designed to deliver charge materials to the furnace quickly, ensuring maximum furnace utilization and efficiency of your induction melt system.
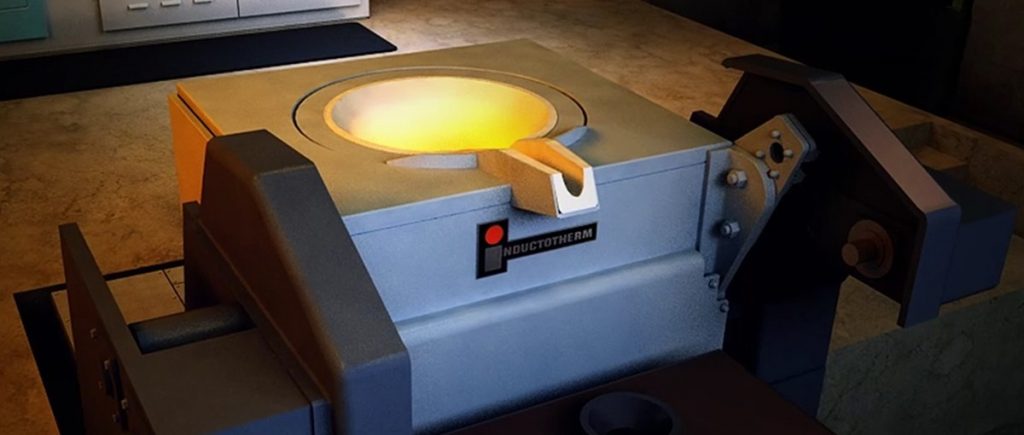
With decades of technological leadership in automated pouring, Inductotherm is helping foundries increase productivity and reduce operating costs.
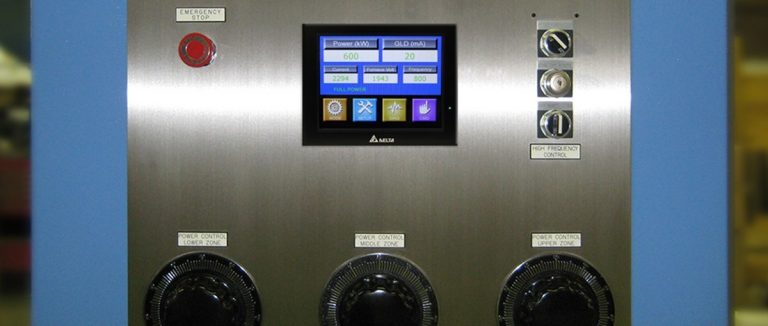
Our world famous family of VIP® induction power systems have the fastest melt rates from cold charge to pouring temperature and melt more pounds per kWh and kVA for lower melting costs and greater productivity.