Aluminum Might Be a Lightweight Metal but Your Equipment Supplier Should be the Industry Heavyweight
Whether you are an aluminum caster, foundry, die caster, recycler or alloy supplier—Inductotherm offers highly efficient and industry proven remelting and alloying furnaces. We can build the ideal induction melting system for virtually any aluminum application.
Induction Offers the Aluminum Industry Many Advantages
Inductotherm is an industry leader in designing and manufacturing technologically advanced systems for virtually all metals and materials, including aluminum. From start to finish, Inductotherm’s aluminum technology works. Converting alumina into pure aluminum and ultimately into useful aluminum alloys is an energy-intensive process which is why energy-efficient furnaces manufactured by Inductotherm have proven their value in aluminum plants worldwide. Inductotherm induction furnace technologies can compete with more conventional methods such as fossil fuel furnaces and resistance furnaces. Induction is practical for all aluminum melting applications and offers many advantages over conventional aluminum melting furnaces.
What Aluminum Applications Can Successfully Benefit From Induction?
- Foundry/Casting
- Aluminum Billet Casters
- Recycling/Remelting
- Diecasting
- Chip Melting
- Investment Casting
- Primary Aluminum
- Secondary Aluminum
Aluminum Chip Melting
Aluminum chips are challenging to melt due to their tendency to float on the surface of the molten aluminum when added to most furnaces.
An aluminum chip melting system utilizing a traditional coreless induction furnace can help overcome this with its inherent stirring. The stirring helps submerge and breakup clumps of aluminum chips, allowing them to be melted more efficiently than a furnace with little or no stirring.
Advantages of Using Induction Melting Technology for Melting and Casting Aluminum:
- Operational flexibility
- Induction furnace systems are smaller and have a more manageable footprint
- Easy to change alloys
- Can immediately shut down if needed without costly repercussions
- Increased Efficiency
- With induction the heat source is the metal itself
- Gas-fired furnaces are about 20% efficient, whereas our Acutrak® DEH System is up to 92% efficient and most induction furnaces are typically 60%
- Better/Cleaner Metal Quality
- Induction melting furnaces do not give off gases
- Gas-fired and combustion furnaces expose the metal to gases and oxygen which add impurities to the metal
- Better Work Environment/Worker Friendly
- With induction melting there is little residual heat and minimal noise
- Gas-fired furnaces give off a lot of heat and combustion furnaces are very noisy
New to Induction? Here is What You Need to Know About How Induction Works
As current flows through an induction coil, a magnetic field is formed. Applying alternating current through this coil will result in a magnetic field changing in direction at the same rate as the frequency of the alternating current. When the aluminum charge material is added, Faraday’s Law takes over. The induced voltage will result in the flow of current through the material in the magnetic field. As current flows through the material, there is resistance to the movement of the electrons. Materials that are more resistant to the flow of electrons will give off more heat as current flows through them. Induction heat is generated in the material of the product by the flow of current. The heat from the product surface is then transferred through the material with thermal conduction.
When the metal becomes molten the magnetic field also causes the bath to move. This is called inductive stirring and it mixes the bath to produce a more uniform mix which assists with alloying. Water cooling systems typically keep the coils cool however since aluminum is a low-temperature metal, our Acutrak® Direct Electric Heat System can be air-cooled making it an excellent option for aluminum melting.
Best Induction Furnaces and Systems for Aluminum
Depending on your application, Inductotherm offers a variety of advanced furnace systems for aluminum melting.
Direct Electric Heat (DEH)
- Precisely controllable induction melting
- Faster, cleaner and more efficient melting
- Self-contained power supply and compact furnace to reduce installation time, effort and cost
- Ideal for diecast, permanent mold, and aluminum foundry operations
- The Acutrak® DEH System is well suited for die casting operations, permanent mold casting and for foundries
Hybrid™ Furnaces
- Proven coreless induction furnace technology
- Additional benefits of a channel furnace uppercase
- Greater alloy flexibility and refractory life
- Allow for inert gas cover, dross removal and quick alloy change
- Ideal for aerospace and commercial slab and billet casting
- Aluminum billet casters may find that our unique Hybrid™ Furnace is an excellent choice for them
Inductotherm’s Traditional Coreless Furnaces
- Coreless induction furnaces offer superior performance and outstanding durability for all your melt shop needs regardless of the size of your foundry
- Able to meet the demanding requirements of investment casters, specialty foundries and the aluminum industry
- Dura-Line® Furnaces are designed to give foundries another choice in small- to medium-sized applications, while our Heavy Steel Shell Furnaces are built tough for the largest foundries
Removable Crucible Furnaces
- Widely used by aluminum melt shops
- Ensure that molten aluminum is always available from one crucible or the other
- Provide great alloy flexibility
- Choose the design and configuration based on your space and operating requirements
- Our removable crucible furnaces Push-out Furnace or a Lift-Swing Furnace can help to ensure that molten aluminum is always available from one crucible or the other
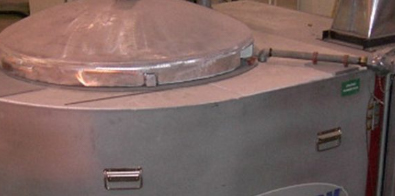
The Acutrak® Direct Electric Heat (DEH) System systems are well suited for die casting operations, permanent mold casting, and for foundries.
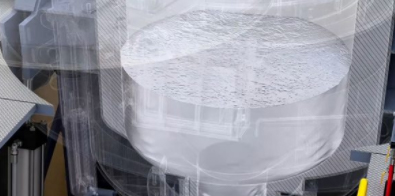
Inductotherm’s Hybrid™ Furnace draws on the design advantages of both the coreless and channel melting holding furnaces.
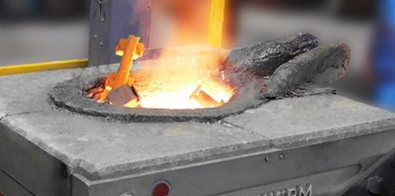
Dura-Line® induction melting furnaces are ideal for when you want big furnace features in a midsize induction furnace melter.
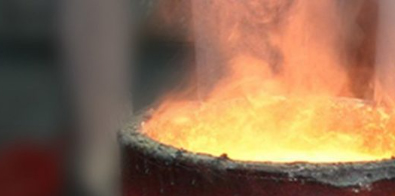
Push-Out Furnaces provide nonferrous and precious metal casters with clean, compact and highly productive crucible melting systems.